You Need Professionals
We now live in a world, at least as far as cars go, where everything affects everything. Even the simplest service done absolutely correctly can result in an unanticipated problem that requires the skills of a master tech to resolve. In other words, a guy who just changes oil will hopefully get very good at changing oil and at avoiding many of the common pitfalls of that service. But at some point, something will happen, most likely not caused by any technical error, but as a result or happenstance of the service.
Here are 3 examples I have seen recently:
The Maxima Mystery 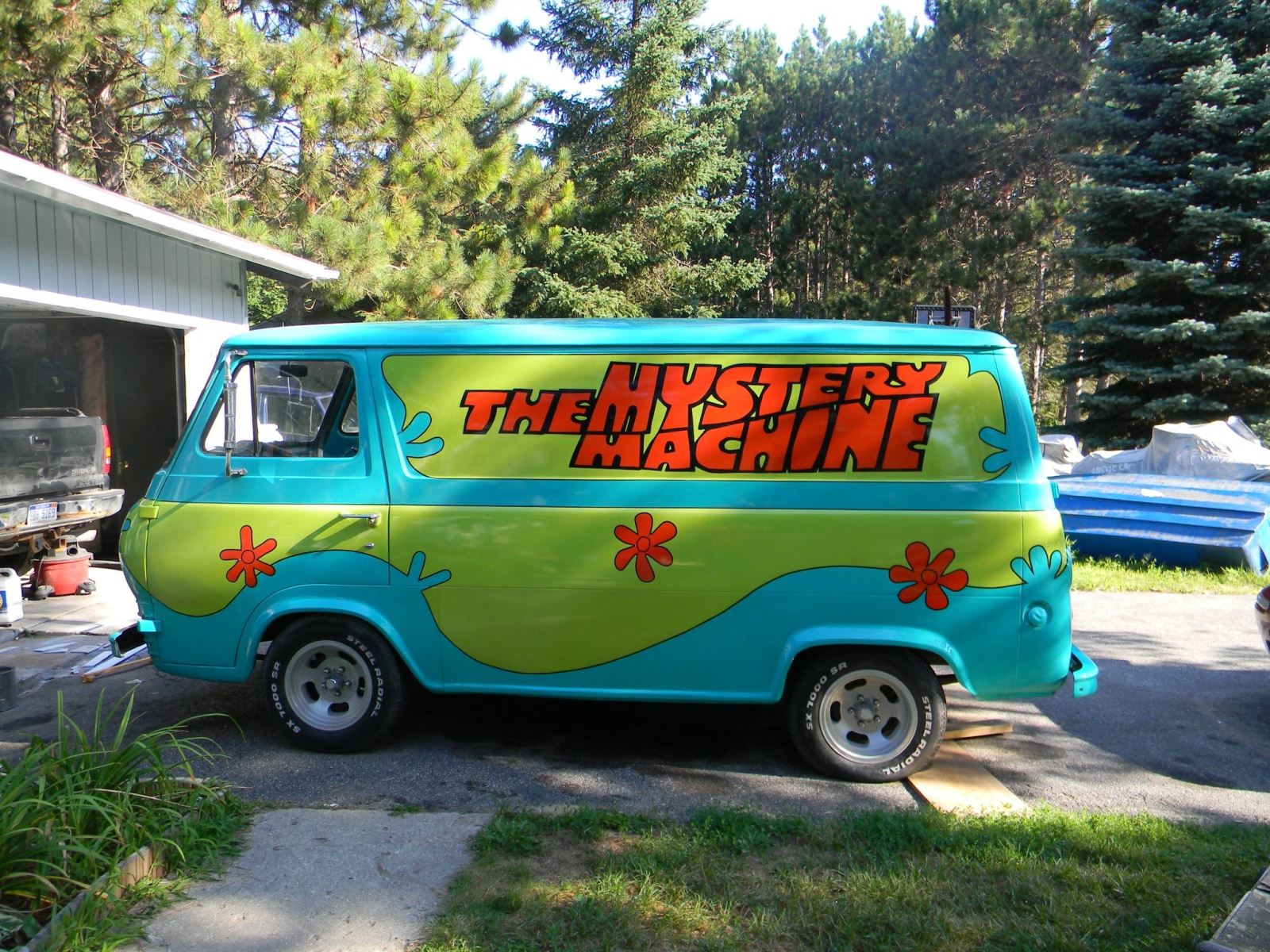
Several Nissan Maximas built in the last decade would come in for a routine oil change. When the oil change was complete and the car was restarted, the check engine light would come on. Even more maddening, it always seemed to wait until the customer drove the car away before coming on. When we’d scan the computer we would find a code indicating a camshaft position sensor out of sync. All tests showed the camshaft sensor in sync, so the technician would clear the code and not see the car again until the next oil change.
After this happened a few times with different cars, I investigated and found that in that moment of startup after the oil change, the timing chain would rattle a few seconds before the hydraulic tensioner pumped up and took the slack out. In just that moment with the chain loose, the ever vigilant computer saw the crankshaft sensor at one end of the chain out of step with the camshaft sensor at the other end of the chain and dutifully sent a code.
Clearly a slow-acting tensioner coupled with a less than perfect oiling system was the root cause of the problem, but I wasn’t about to tell people they needed an expensive timing chain job on a 100,000 mile engine. So I instituted a policy of priming the oiling system by filling the oil filter with oil prior to installation, cranking the engine with the computer disabled to build up pressure, and running a mandatory five-minute test drive to make sure the light wasn’t going to come on.
Make a Hard Left...
A family member’s Chrysler PT Cruiser came to me with bad steering/suspension problems. Tires worn down to metal on the edges, pulling, shaking, and unstable. I had it checked and found it needed shocks on the rear, front control arms (the bushings were gone), and at least two tires. The shocks and tires got done but the control arms hadn’t come in, and it was the only car I had to get home in. So against my better judgment I drove it. And it drove okay.
The next day the control arms came in and were installed and the alignment set. Now it should be like new. As I set off to test drive, it drove beautifully. Until the transmission shifted and the car gave a nasty tug to the left… and did so at every shift or change of torque. How could new control arms cause that? They didn’t. They caused an already existing problem to become apparent. A torque mount (a thick aluminum piece connecting the engine to the frame) was actually broken, but you couldn’t see the break unless a lot of torque was applied. This allowed the whole engine and transmission to shift several inches and tug the steering through the drive axles. When the control arms were bad there was enough slack that the gryroscoping effect of the wheels rolling was great enough to keep it straight even when the axles tugged. When we took that slack out the problem became very apparent.
Patience with a Prius
Just recently a very high-mileage Prius was in the shop getting struts, alignment, and maintenance. The car shut down in the parking lot and refused to move, acting like a petulant child throwing a temper tantrum in a supermarket. One of the things that separates professionals from amateurs in business and sports is that when things don’t go right, amateurs panic; professionals remain calm and analyze the problem scientifically. The first thing you need is time. The issue was explained to the customer as best we could with the little information gathered. The customer, who was very understanding, allowed us the time needed to sort out what was going on.
The car’s computer codes indicated poor performance from the gasoline engine and a failure of the gasoline engine to start. Every indication was that the gasoline engine would start and run for 15 seconds and then cut off. But that was an illusion. The unconventional design of the Prius does not use a conventional starter (an electric motor with a gear turning another gear on the engine flywheel), which is what gives the classic sound we all hear when an engine is trying to start. The Prius uses the powerful electromagnet in the generator system to spin the engine to start, which make no mechanical noise. So you hear the engine and it sounds like it’s running, but it’s just in the trying-to-start cycle. Once that hurdle was cleared, the problem was now simplified to the gasoline engine. Testing revealed a bad reading from the air flow sensor.
The tech removed and cleaned the sensor and the car became itself again. Did the sensor just choose that moment to malfunction? Did a microscoping piece of debris fall in it when the air filter was checked? Not important to me or the customer. What’s important is that the technician, when given the time and resources, accurately identified and corrected the problem.
Anyone who works in a shop that handles a high volume of cars and says that they never encounter unexpected problems is not telling the truth. Cars are complex machines and everything affects everything. That’s why for even the simplest service, be it an oil change, tire rotation, or vehicle inspection, you want your car – the first or second largest asset most people own – in the hands of professionals, so that whatever comes up, expected or unexpected, it can be handled professionally.
By Doug Flint